DATASHEET
POWDERRANGE® H13
Applicable specifications: DIN EN ISO 4957 Grade 1.2344/X40CrMoV5-1
Associated specifications: ASTM A681, JIS G4404
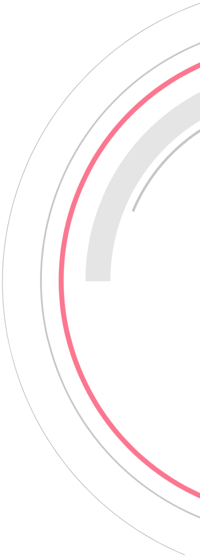
Type analysis
Single figures are nominal except where noted.
Iron | Balance |
Silicon | 0.80–1.20 % |
Manganese | 0.25–0.50 % |
Phosphorus | 0.03 % |
Chromium | 4.80–5.50 % |
Vanadium | 0.80–1.15 % |
Nitrogen | 0.10 % |
Sulfur | 0.02 % |
Molybdenum | 1.10–1.50 % |
Carbon | 0.35–0.42 % |
Oxygen | 0.10 % |
Description
PowderRange® H13 is a versatile air hardening, 5% chromium hot work steel. It exhibits a good combination of high toughness, temper resistance, and thermal fatigue resistance. PowderRange® H13 has challenging weldability in laser and electron-beam additive manufacturing processes, where part geometry and build parameters could induce micro-cracking.
Key Properties
- High impact toughness and good ductility
- High temperature strength
- Good abrasion resistance at temperature
- Resistance to thermal fatigue
- Limited distortion during hardening
Markets
Applications:
- Tooling for extrusion and molding
- Valves and fittings
- Pumps and impellers
- Manifolds
- Die casting
Powder properties
Part Number | PowderRange® H13 |
Application | L-PBF1 |
Maximum Particle Size | Max 1 wt% > 53 µm2 |
Minimum Particle Size | Max 10 vol% < 15 µm3 |
LSD Percentile | D10, D50, D903, reported |
Atomization | Vacuum Induction Melted, Nitrogen Gas Atomized |
Apparent Density (G/CM3) | Measured according to ASTM B2124 and reported |
Hall Flow (S/50G) | Measured according to ASTM B2135 and reported |
1ASTM/ISO 52900: Laser—Powder Bed Fusion (L-PBF), Electron-Beam Powder Bed Fusion (EB-PBF), Directed Energy Deposition (DED)
2ASTM B214 Standard Test Method for Sieve Analysis for Metal Powders
3 ASTM B822 Standard Test Method for Particle Size Distribution of Metal Powders and Related Compounds by Light Scattering
4 ASTM B212 Standard Test Method for Apparent Density of Free-Flowing Metal Powders Using the Hall Flowmeter Funnel
5 ASTM B213 Standard Test Method for Flow Rate of Metal Powders Using the Hall Flowmeter Funnel
Testing of powder will fulfill certification requirements to Nadcap Materials Testing and ISO/IEC 17025 Chemical, per relevant ASTM procedures
For additional information, please
contact your nearest sales office:
The mechanical and physical properties of any additively-manufactured
material are strongly dependent on the processing conditions used to
produce the final part. Significantly differing properties can be obtained by
utilizing different equipment, different process parameters, different build
rates and different geometries. The properties listed are intended as a
guide only and should not be used as design data.
The information and data presented herein are typical or average values
and are not a guarantee of maximum or minimum values. Applications
specifically suggested for material described herein are made solely for the
purpose of illustration to enable the reader to make his/her own evaluation
and are not intended as warranties, either express or implied, of fitness for
these or other purposes. There is no representation that the recipient of
this literature will receive updated editions as they become available.
Unless otherwise specified, registered trademarks are property of
CRS Holdings Inc., a subsidiary of Carpenter Technology Corporation.
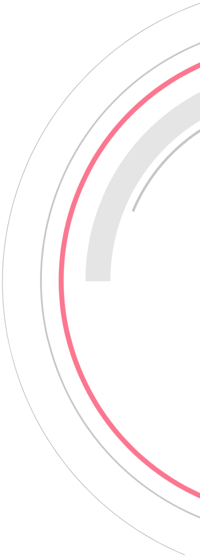